Carestream Sign In
Welcome to Carestream.com's communities.
Our customers and partners have access to powerful online communities and tools. Use this overview to discover the best destination for you. Registration and sign-in are required to access these websites.
Vue Cloud Community
Carestream's Vue Cloud Community is your single point of access to the tools you need to diagnose exams, review a patient portfolio or view real-time department performance.
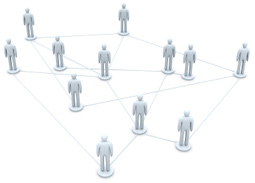
Carestream.com Communities and Tools
Welcome to Carestream.com's communities.
Our customers and partners have access to powerful online communities and tools. Use this overview to discover the best destination for you. Registration and sign-in are required to access these websites.
Vue Cloud Community
Carestream's Vue Cloud Community is your single point of access to the tools you need to diagnose exams, review a patient portfolio or view real-time department performance.
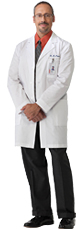
Process Control Procedure for Mammographic Processors
ITEMS NEEDED
- Sensitometer with 21 density steps.
- Densitometer.
- Thermometer ( not mercury) with accuracy of ± 0.50°F (±0.30°C).
- Fresh box of 18 x 24cm film, the same as that used for mammography.
- Control charts such as the Carestream Mammography Processing Control Chart Mammography Processing Control Chart (pdf) (Cat. No. 1801398, publication number M7-173).
ESTABLISHING THE BASELINE
- Ensure that:
- the processor is thoroughly clean and functioning properly
- the processor is filled with properly mixed fresh chemicals
- the proper amount of developer starter has been added
- the proper developer temperature and replenishment rates have been set.
- Set aside a fresh box of 18 x 24cm film that is used for mammography. Designate it as your "QC" film and record the complete emulsion number on the control chart.
- Set the sensitometer for the appropriate film spectral sensitivity (green) and for single-emulsion film.
- On five (5) consecutive days, expose a sensitometric strip using film from the "QC" box; process immediately. Note that:
- the processor must be at the right temperature
- the probe of the thermometer should be placed consistently in the same area on the non-drive side of the processor developer tank
- single-emulsion film must be inserted into the sensitometer so the emulsion side faces the light-exposing source
- the sensitometric strip must be consistently fed into the processor so that the less-exposed end is fed first.
- On the fifth day, use the densitometer to read the 21 density steps on each processed film. NOTE: Take the reading from the middle of each step.
- Average the values of the 21 steps for the five days.
DETERMINING MID-DENSITY (MD)
- Determine which step has an average density closest to 1.20. Designate this step as the mid-density (MD) step for all future MD determinations and record the step number on the chart.
- Write the average MD value on the middle line.
DETERMINING DENSITY DIFFERENCE (DD)
- Select the step with the average density closest to 2.20.
- Select the step with the average density closest to, but not less than, 0.45.
- Subtract the density value determined in step 2 from the density value determined in step 1. This value will be the density difference (DD).
- Designate the two steps as those to be used for all future DD determinations and record the step numbers on the chart. Write the average DD value on the middle line.
DETERMINING BASE + FOG
- The five-day average of the least-exposed step (usually the first step) determines the Base + Fog of the film. (Any clear area of the film may also be used to determine Base + Fog.)
- Write the average Base + Fog value on the middle line.
DEVELOPER TEMPERATURE
- On the middle line, write the developer temperature recommended by the film manufacturer for your:
- type of film
- developer (chemicals)
- processor
- length of developer immersion time.
ESTABLISHING OPERATING LIMITS
- The preferred mammography MD and DD operating limits are ± 0.10. The maximum outermost limits are ± 0.15 .
- Add 0.10 and 0.15 to the values on the middle line for MD and DD; write the preferred and maximum upper limits on the control chart.
- Subtract 0.10 and 0.15 from the values on the middle line for MD and DD; write the preferred and maximum lower limits on the control chart.
- Add 0.03 to the value on the middle line for Base + Fog; write the upper limit on the control chart. (There is no lower limit for Base + Fog.)
DAILY PROCESSOR QUALITY CONTROL
- Expose and process a sensitometric strip each morning that mammography films will be processed.
- Use the densitometer to read the values for MD, DD and Base + Fog, using the same steps recorded on the control chart.
- Plot the MD, DD, Base + Fog, and measured temperature values on the control chart.
- Evaluate the results and make any necessary adjustments before processing any films.
EVALUATING THE CONTROL CHART
Points that are plotted on the control chart for MD and DD that are within the ±0.10 control limits should be considered normal process variations.
- If any points are plotted on the control chart for MD and DD between ± 0.10 and ± 0.15, expose and process another sensitometric strip for comparison. Mammography films may be processed. The processor should be closely monitored to make certain that the outermost limits are not exceeded.
- If any plotted points on the control chart for MD and DD reach or exceed ± 0.15, expose and process another sensitometric strip for comparison. If the same results are obtained, no mammography films may be processed until the cause is determined and corrected. Plot the results obtained after the process has been brought back "in control." Note the action(s) taken to achieve this in the "Remarks" section on the control chart.
- Any points plotted for Base + Fog that are within 0.03 are considered to be normal process variations; any points plotted for Base + Fog that exceed + 0.03 require immediate analysis.
- The developer temperature should remain as close as possible to the temperature recommended by the film manufacturer; it should not vary by more than ±0.50°F (±0.30°C).
- A trend exists if a series of consecutive points (three or more) progress steadily upward or downward. Such a trend may be a shift taking place slowly and visibly with respect to time. Monitor the processor closely.
- Trends or gross fluctuations should be noted and evaluated. If necessary, appropriate action should be taken.
- The "Remarks" section of the control chart should be used to note reasons for fluctuations such as routine preventive maintenance, fresh chemicals or developer starter added, etc.
FINAL COMMENTS
It is recommended that a processor maintenance log be kept for each processor to record all service on the unit. This log can be used to correlate processor service with processor performance. The calibration of the sensitometer, densitometer and thermometer should be checked periodically according to the recommendations, where available, of the manufacturer. The Mammography Processing Control Chart may be used in various ways to monitor processor performance. For example, a new chart may be used for each month or information may be plotted continuously and a new chart started every 31 days.
Choose a Region
- Africa
- Asia Pacific
- GCC-TEST
- Europe
- Middle East
- North America
- South America
Africa
Asia Pacific
GCC-TEST
Europe
Serbia
Slovakia Slovenia Spain Sweden Switzerland Ukraine United Kingdom |
Middle East
North America
South America
São Vicente and Granadina
Suriname Trinidad and Tobago Turk and Caicos Islands Uruguay U.S. Virgin Islands Venezuela Virgin Islands (British) |